The world of industry and manufacturing is undergoing a significant metamorphosis, driven by rapid advances in digital technologies. Coined as Industrial Digital Transformation (IDT), this paradigm shift is ushering in a new era characterized by increased efficiencies, improved products, and innovative business models. As industries continue to embrace digital tools, the landscape of manufacturing and production is changing profoundly. In this article, we’ll dive deep into Industrial Digital Transformation and discover multiple aspects of this term in order to provide a comprehensive understanding to manufacturing businesses.
Table of Contents
Definition of Industrial Digital Transformation
Industrial Digital Transformation refers to the integration of digital technologies, data analytics, and automation into various aspects of industrial processes, operations, and business models to improve efficiency, productivity, and competitiveness. It involves the application of digital technologies such as the Internet of Things (IoT), artificial intelligence (AI), machine learning, big data analytics, cloud computing, and advanced robotics to transform traditional industrial sectors.
Importance of Industrial Digital Transformation
Industrial Digital Transformation is of paramount importance in today’s rapidly evolving business landscape. It serves as a catalyst for innovation and competitiveness across various industrial sectors. One of its primary benefits is the ability to drive efficiency gains through the integration of digital technologies, data analytics, and automation. By connecting machines, devices, and systems, businesses can monitor operations in real-time, predict equipment failures, and optimize processes, leading to reduced downtime and increased productivity. Furthermore, the insights gained from data analytics enable informed decision-making, which is crucial for staying agile in a dynamic market.

Additionally, Industrial Digital Transformation enhances sustainability efforts by optimizing resource usage, reducing energy consumption, and minimizing waste. It also contributes to improved product quality and customization, allowing businesses to meet changing customer demands more effectively. Moreover, by embracing digital transformation across industries, companies can explore new revenue streams and business models, including subscription-based services and value-added offerings.
Furthermore, in an interconnected world, cybersecurity becomes paramount. Industrial Digital Transformation necessitates robust cybersecurity measures to safeguard sensitive data and critical infrastructure, ensuring the continuity and security of operations.
Ultimately, Industrial Digital Transformation isn’t merely a technological upgrade but a strategic imperative. It enables businesses to remain competitive, resilient, and responsive in an increasingly digital and interconnected global economy. Those who embrace this transformation are better positioned to adapt to market changes, deliver higher-quality products and services, and build sustainable, future-ready enterprises.
Key Technologies Driving Industrial Digital Transformation
Internet of Things (IoT)
IoT, or the Internet of Things, has emerged as a pivotal technology driving transformation across various industries. Its impact can be seen in several key ways.
IoT has revolutionized data collection and monitoring. By connecting everyday objects, machines, and devices to the internet, organizations can gather an unprecedented volume of real-time data. This data offers valuable insights into processes, performance, and customer behavior. In manufacturing, for instance, IoT sensors can track the status of machinery, enabling predictive maintenance to reduce downtime and improve efficiency. In agriculture, IoT devices can monitor soil conditions, weather patterns, and crop health, optimizing yields and resource utilization. This data-driven decision-making is a cornerstone of digital transformation.

Moreover, IoT fosters automation and efficiency. It allows for remote control and management of devices and systems, reducing the need for human intervention. For instance, in smart buildings, IoT-enabled HVAC systems can adjust temperatures based on occupancy and weather forecasts, leading to energy savings. In logistics and supply chain management, IoT helps track the location and condition of goods in real time, optimizing routes and ensuring the timely delivery of products. These efficiencies not only lower operational costs but also improve overall customer experiences.
Another crucial aspect of IoT is its role in enabling new business models and services. Companies are leveraging IoT to offer value-added services. In healthcare, wearable IoT devices can collect patient data and send it to healthcare providers for remote monitoring, improving patient care. In the automotive industry, IoT-enabled vehicles can provide services such as predictive maintenance alerts, real-time traffic updates, and even autonomous driving features. These innovative services not only create new revenue streams but also enhance customer loyalty.
Big Data and Analytics
One of the most significant contributions of Big Data Analysis is its ability to process and derive insights from vast and complex datasets that were previously unmanageable. This capability has enabled companies to gain a deeper understanding of their operations, customers, and markets.
Big Data Analysis has empowered businesses to make data-driven decisions. By collecting and analyzing data from various sources, including customer interactions, online behavior, and operational processes, organizations can uncover valuable insights. These insights inform strategic planning, product development, and marketing strategies. They allow companies to tailor their offerings to customer preferences, optimize supply chains, and improve overall efficiency.

Additionally, Big Data Analysis has played a pivotal role in enhancing customer experiences. With a better understanding of customer behavior and preferences, businesses can offer personalized recommendations, targeted advertising, and customized products or services. This not only leads to increased customer satisfaction but also drives higher sales and customer retention rates.
Moreover, Big Data Analysis has been instrumental in predictive analytics. By identifying trends and patterns within large datasets, organizations can forecast future events, such as equipment failures or market trends. This predictive capability is particularly valuable in industries like manufacturing, where it enables proactive maintenance and minimizes downtime, ultimately reducing costs and increasing productivity.
In the healthcare sector, Big Data Analysis has transformed patient care through predictive analytics and precision medicine. It allows for the analysis of vast patient datasets to identify potential diseases, optimize treatment plans, and develop personalized therapies, leading to better patient outcomes.
Artificial Intelligence and Machine Learning
Artificial Intelligence (AI) and Machine Learning (ML) have emerged as key technologies driving transformation across various industries, revolutionizing the way businesses operate and make decisions. These technologies have had a profound impact in several ways.
AI and ML enable businesses to harness the power of data like never before. With the vast amounts of data generated in today’s digital world, AI and ML algorithms can analyze this data to uncover valuable insights, trends, and patterns that were previously impossible to detect. This data-driven decision-making empowers organizations to make more informed choices, optimize processes, and enhance overall efficiency.

Secondly, AI and ML have become essential tools for automation. They can automate repetitive tasks, allowing employees to focus on more creative and strategic endeavors. In manufacturing, for example, AI-powered robots can handle repetitive assembly tasks, leading to increased production rates and reduced errors. In customer service, chatbots and virtual assistants handle routine queries, freeing up human agents to address more complex issues.
Moreover, AI and ML are instrumental in predictive analytics. By analyzing historical data, these technologies can forecast future trends and events with remarkable accuracy. This capability is particularly valuable in supply chain management, where predicting demand and optimizing inventory levels can lead to significant cost savings and improved customer service.
AI and ML also play a critical role in personalization and customer experience. They enable businesses to tailor their products, services, and marketing efforts to individual customer preferences. This level of personalization fosters customer loyalty and drives revenue growth. For instance, recommendation algorithms used by streaming services and eCommerce platforms suggest content and products based on a user’s previous interactions.
Cloud Computing
Cloud computing has emerged as one of the key technologies driving transformation across various industries. Its impact is profound, with several transformative aspects that have reshaped how businesses operate and leverage technology.
First and foremost, cloud computing has democratized access to advanced computing resources. It has allowed even small and medium-sized enterprises to access powerful computing capabilities and storage on a pay-as-you-go basis, eliminating the need for significant upfront investments in infrastructure. This accessibility has leveled the playing field, enabling businesses of all sizes to compete effectively in the digital age.
Cloud computing has also facilitated scalability and agility. Organizations can easily scale their computing resources up or down based on demand, making it possible to handle massive workloads during peak times and scale down during periods of lower activity. This flexibility enables businesses to respond rapidly to changing market conditions and customer demands.

Moreover, cloud computing has fostered innovation through easier experimentation and development. With cloud-based platforms and services, developers can quickly prototype and launch new applications and services without the constraints of traditional infrastructure. This has accelerated the pace of innovation, allowing businesses to bring new products and services to market faster.
Cloud computing has played a pivotal role in data analytics and machine learning. It provides the computational power and storage required to analyze vast datasets and train complex AI models. This has fueled advancements in data-driven decision-making, predictive analytics, and AI-driven automation, enabling organizations to gain valuable insights and optimize their operations.
Security and compliance are also areas where cloud computing has made strides. Many cloud providers invest heavily in robust security measures, data encryption, and compliance certifications. This has helped businesses enhance their cybersecurity posture and meet regulatory requirements more effectively.
Automation and Robotics
Automation and Robotics have emerged as pivotal technologies driving transformation across various industries. Their impact is profound, reshaping the way businesses operate and deliver products and services.
One of the primary ways automation and robotics contribute to transformation is through increased efficiency and productivity. Automated systems can perform repetitive tasks with precision and consistency, significantly reducing the margin of error. In manufacturing, for instance, robots can assemble products faster and more accurately than human workers, leading to higher production output and improved quality. This efficiency translates into cost savings and a competitive advantage.
Moreover, automation and robotics are at the forefront of operational optimization. In logistics and supply chain management, autonomous robots are used to streamline warehouse operations, enhancing inventory management and order fulfillment processes. This not only reduces operational costs but also accelerates delivery times, meeting the growing demands for quick and reliable services.

These technologies enable predictive maintenance, which is a game-changer for asset-intensive industries. Sensors and data analytics integrated into machines can monitor their performance in real time and predict potential failures. This proactive approach minimizes downtime, extends the lifespan of equipment, and reduces maintenance costs, providing substantial economic benefits.
Automation and robotics also play a crucial role in enhancing workplace safety. Dangerous and repetitive tasks can be assigned to robots, protecting human workers from harm and allowing them to focus on more complex and creative aspects of their jobs. In industries like healthcare, robotic surgery assists surgeons in performing intricate procedures with precision, reducing patient risk.
Furthermore, the combination of automation and data-driven decision-making enables industries to adapt to market dynamics rapidly. With instant access to data analytics, businesses can make informed decisions, optimize processes, and respond swiftly to changing customer preferences and market trends. This agility is essential for staying competitive in today’s fast-paced business environment.
Benefits and Opportunities
Enhanced Operational Efficiency
First and foremost, Industrial Digital Transformation enables real-time monitoring and data analysis. With IoT sensors and connected devices embedded in equipment and machinery, industries can gather massive amounts of data on their processes. This data is then analyzed using advanced analytics and machine learning algorithms to identify inefficiencies, predict potential issues, and optimize operations. This level of insight allows for proactive decision-making, reducing downtime, and improving resource allocation.
Furthermore, automation plays a pivotal role in enhancing operational efficiency. Automated systems and robotics can take on repetitive, manual tasks, minimizing errors and increasing productivity. In manufacturing, for instance, robots can work alongside human employees or even replace them in tasks that are hazardous or require precision beyond human capabilities. This not only boosts efficiency but also ensures a safer working environment.

Supply chain management also benefits significantly from Industrial Digital Transformation. Companies can use digital technologies to track the movement of goods, manage inventory more effectively, and improve demand forecasting. This leads to reduced lead times, minimized inventory costs, and better customer service through timely deliveries.
Another aspect is predictive maintenance. By continuously monitoring the condition of equipment and using AI algorithms to predict when maintenance is needed, companies can avoid costly unplanned downtime. This not only saves money but also extends the lifespan of machinery and equipment, reducing the need for frequent replacements.
Data-Driven Decision Making (DDDM)
One of the primary benefits of DDDM in Industrial Digital Transformation is improved efficiency. By continuously monitoring and analyzing data from sensors, machinery, and processes, companies can identify bottlenecks, inefficiencies, and underperforming assets. This insight allows for timely adjustments and optimizations, resulting in increased productivity and reduced downtime. For example, predictive maintenance, made possible by data analytics, can help anticipate equipment failures before they occur, minimizing costly disruptions.
Another advantage is enhanced product quality and consistency. DDDM enables industries to monitor and control production processes with greater precision, ensuring that products meet or exceed quality standards. This not only boosts customer satisfaction but also reduces waste and the need for rework, ultimately leading to cost savings.

Furthermore, DDDM opens the door to more responsive and customer-centric operations. By analyzing customer data and feedback, companies can tailor their products and services to meet specific customer needs and preferences. This personalization fosters stronger customer relationships and can lead to increased sales and market share.
Moreover, DDDM provides a foundation for innovation and business growth. Industries can identify emerging trends, market opportunities, and areas for product development through data analysis. This strategic advantage allows companies to diversify their offerings, enter new markets, and adapt quickly to changing industry landscapes.
Predictive Maintenance and Reduced Downtime
Predictive Maintenance and Reduced Downtime are significant benefits and opportunities that have emerged from Industrial Digital Transformation.
Predictive Maintenance: In traditional industrial settings, maintenance tasks often follow a fixed schedule or are performed reactively when equipment fails. This approach is costly and can lead to unnecessary downtime. Industrial Digital Transformation has revolutionized maintenance practices by enabling predictive maintenance. Through sensors and data analytics, companies can continuously monitor the condition of machinery and equipment in real-time. This data is used to predict when maintenance is needed, based on actual usage and wear-and-tear, rather than arbitrary schedules. As a result, maintenance becomes more efficient, costs are reduced, and machinery downtime due to unexpected breakdowns is minimized. This proactive approach not only saves money but also extends the lifespan of equipment.
Reduced Downtime: One of the most significant opportunities arising from Industrial Digital Transformation is the dramatic reduction in downtime. Downtime in industrial operations can be incredibly costly, resulting in lost production, revenue, and customer trust. With real-time data monitoring and predictive analytics, companies can identify and address potential issues before they lead to breakdowns. This means that maintenance activities are planned during scheduled downtime, rather than in the midst of urgent repairs. Additionally, automation and remote monitoring capabilities allow for quicker responses to issues, often without the need for human intervention. As a result, the overall downtime is reduced, production efficiency is improved, and businesses can meet customer demands more consistently.
Improved Product Quality and Innovation
Industrial Digital Transformation has led to a substantial improvement in product quality. By integrating digital technologies into manufacturing processes, companies can monitor and control production more precisely. Real-time data from sensors and equipment provide insights into product parameters, enabling quick adjustments and quality assurance. For example, in the automotive industry, digital sensors and AI-powered quality control systems can detect defects or deviations in real time, ensuring that only high-quality products reach customers. This not only reduces defects and recalls but also enhances customer satisfaction and trust in the brand.
Secondly, Industrial Digital Transformation has fueled innovation across various industries. With access to vast amounts of data and advanced analytics, companies can identify trends, consumer preferences, and market opportunities more accurately. This data-driven approach allows for the development of innovative products and services that are better tailored to customer needs. For instance, in healthcare, the adoption of digital health technologies has given rise to telemedicine, wearable devices, and personalized treatment plans, revolutionizing patient care.
Furthermore, digital technologies have streamlined research and development processes. Simulation and modeling software can accelerate product prototyping and testing, reducing time-to-market for new innovations. This agility fosters a culture of continuous improvement and innovation within organizations.
Additionally, the integration of IoT and smart devices has enabled the creation of interconnected ecosystems, fostering innovation through collaboration. For example, in agriculture, IoT sensors, drones, and data analytics are helping farmers optimize crop yields and resource usage, contributing to sustainable and innovative farming practices.
Supply Chain Optimization
Real-time visibility across the entire supply chain is now attainable. IoT sensors and connected devices enable the monitoring of goods, shipments, and inventory at every stage. This visibility allows for better decision-making by anticipating disruptions, such as delays or quality issues and responding proactively. It minimizes the risk of stockouts and overstock situations, reducing carrying costs while ensuring products are available when and where they are needed.
Secondly, data analytics and AI-powered algorithms are used to optimize supply chain processes. These technologies can predict demand patterns, identify cost-saving opportunities, and improve forecasting accuracy. AI can also optimize transportation routes, reducing fuel consumption and emissions while ensuring timely deliveries. This leads to significant cost savings and a more sustainable supply chain.

Moreover, Industrial Digital Transformation enables supply chain automation. Robotic process automation (RPA) can handle routine tasks like order processing, invoicing, and data entry, reducing human error and speeding up processes. This frees up human resources to focus on more strategic and complex tasks, enhancing overall efficiency.
Additionally, by leveraging blockchain technology, companies can enhance transparency and traceability within the supply chain. This is particularly crucial for industries where provenance and compliance are critical, such as pharmaceuticals or food. Customers and stakeholders can access real-time information about the journey of a product, ensuring authenticity and compliance with standards and regulations.
Challenges and Considerations
Legacy Systems and Integration Issues
Legacy systems and integration issues pose significant challenges in the journey of Digital Transformation of industries. Many industrial organizations have decades-old infrastructure and software systems that were not designed to accommodate modern digital technologies. These legacy systems are often characterized by their rigidity, limited data-sharing capabilities, and outdated technology stacks. Integrating them with new digital solutions can be complex and resource-intensive.
One of the primary challenges is interoperability. Legacy systems often use proprietary protocols and formats that do not easily communicate with modern, open-source digital technologies. Bridging this gap requires extensive development efforts and can introduce compatibility issues. It’s essential to ensure that new digital tools can seamlessly connect with existing systems to avoid disruptions in operations.
Security is another critical concern. Legacy systems may lack the robust cybersecurity features needed to protect against modern threats. As organizations integrate digital technologies, they must carefully assess and enhance security measures to safeguard sensitive data and critical infrastructure.

Data migration is a significant consideration as well. Legacy systems may contain vast amounts of valuable historical data. Transferring this data into new digital platforms while maintaining data integrity and ensuring its usefulness can be a complex task.
Additionally, the cost associated with upgrading or replacing legacy systems can be substantial. Organizations need to weigh the benefits of Industrial Digital Transformation against the investment required and establish a clear ROI (Return on Investment) strategy.
To address these challenges, companies planning Industrial Digital Transformation should consider several key factors:
- Comprehensive Assessment: Begin by conducting a thorough evaluation of existing systems and infrastructure. Identify which legacy systems can be upgraded, which need replacement, and which can be integrated with new technologies.
- Interoperability Standards: Choose digital solutions and platforms that adhere to widely accepted interoperability standards to simplify integration and reduce compatibility issues.
- Data Strategy: Develop a robust data strategy to manage data migration, storage, and analytics. Ensure that legacy data is effectively leveraged to drive insights and improvements.
- Cybersecurity: Prioritize cybersecurity measures by implementing modern security protocols and practices to protect both legacy and new digital systems.
- Cost-Benefit Analysis: Assess the costs and potential benefits of Industrial Digital Transformation projects to make informed decisions about investments and prioritize initiatives that offer the most significant returns.
- Phased Implementation: Plan for a phased approach to minimize disruptions. Gradually integrate digital technologies, starting with critical areas, and ensure that employees receive the necessary training and support.
Data Security and Privacy Concerns
As industries increasingly adopt digital technologies and rely on data for decision-making and automation, safeguarding sensitive information becomes paramount.
Firstly, the interconnected nature of Industrial IoT and digital systems creates vulnerabilities. The more devices and sensors are connected, the larger the attack surface for cybercriminals. Industrial systems are attractive targets for cyberattacks due to the potential for widespread disruption, making robust cybersecurity measures essential. Data breaches not only compromise sensitive business information but can also endanger worker safety and disrupt production processes.

Data security and privacy are not just technical issues but also organizational and cultural challenges. Many businesses struggle to implement robust cybersecurity practices and instill a culture of data security throughout their workforce. The lack of cybersecurity expertise and resources can further exacerbate these challenges.
To address these concerns, companies undergoing Industrial Digital Transformation must prioritize data security and privacy considerations. They should implement comprehensive cybersecurity measures, including encryption, network segmentation, and intrusion detection systems. Regular security audits and employee training are essential components of a proactive approach to cybersecurity.
Organizations must adopt a privacy-by-design approach, embedding data protection principles into the development of digital systems. This involves anonymizing and minimizing data collection, obtaining explicit consent when necessary, and ensuring transparency in data practices.
Workforce Skill Gaps and Change Management
Workforce Skill Gaps and Change Management are two critical challenges that organizations encounter during Digital Transformation by industry.
Workforce Skill Gaps
One of the primary challenges in implementing Industrial Digital Transformation is the existence of skill gaps within the workforce. The rapid integration of advanced digital technologies often requires employees to acquire new skill sets. Many existing employees may lack the necessary expertise in areas such as data analytics, programming, or operating and maintaining digital systems. Addressing these skill gaps is essential to fully harness the benefits of the digital transformation industry.
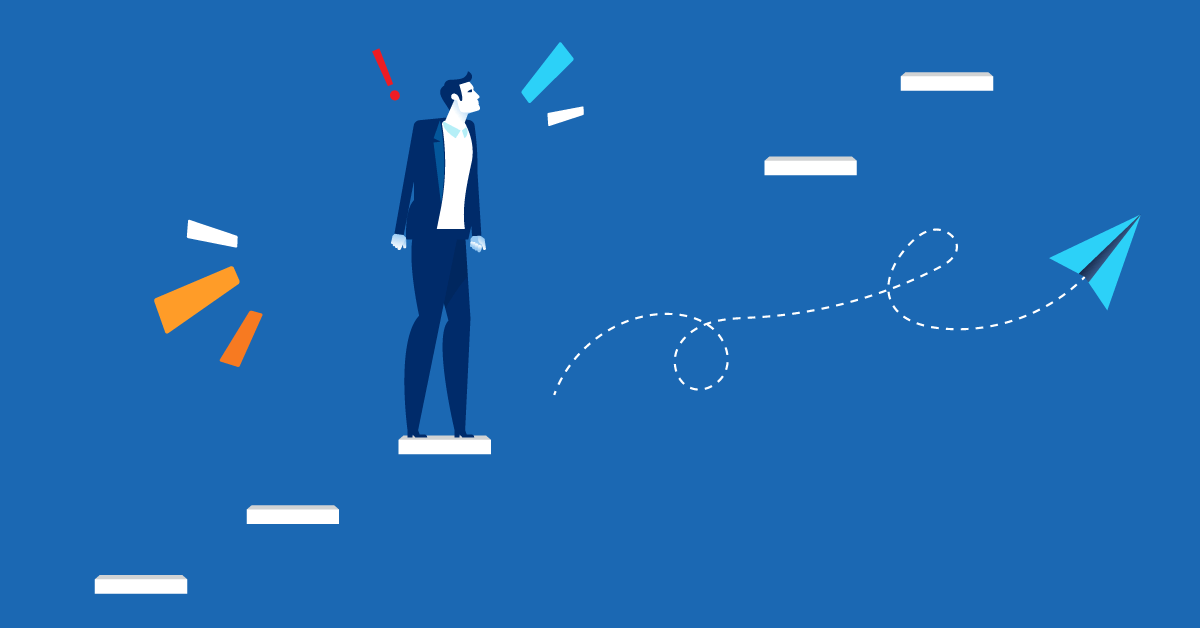
Organizations need to invest in training and upskilling programs to equip their employees with the skills needed to operate, maintain, and innovate with digital technologies. This may involve partnering with educational institutions or hiring new talent with the required expertise. It’s crucial to create a culture of continuous learning and provide ongoing support for employees as technology evolves.
Change Management
Another significant challenge in Industrial Digital Transformation is managing the cultural and organizational changes that come with adopting new technologies and processes. Resistance to change can be a formidable barrier, as employees may be apprehensive about the disruption to their familiar routines and roles.
Effective change management strategies are essential to navigate this challenge. This includes clear communication about the goals and benefits of the transformation, involving employees in the decision-making process, and addressing their concerns. Leadership should set a clear vision and provide the necessary resources to support the transition. Encouraging a culture of innovation and adaptability within the organization can also help employees embrace the changes more readily.
Considerations for Industrial Digital Transformation should include assessing the current skill levels of the workforce, identifying skill gaps, and developing a comprehensive training plan. Organizations should also create a well-defined change management strategy that encompasses communication, employee engagement, and leadership support. By addressing these challenges proactively, organizations can better position themselves to succeed in the digital age and ensure that their workforce is prepared for the future of work.
Advice for Organizations Embarking on the Industrial Digital Transformation Journey
Embarking on the digital transformation journey is a significant endeavor for any organization. To ensure a successful transition and maximize the benefits of digital transformation, consider the following advice:
- Clearly Define Objectives and Goals: Begin by establishing clear and measurable objectives for your digital transformation. What specific outcomes are you looking to achieve? Whether it’s improving efficiency, enhancing customer experiences, or entering new markets, having well-defined goals will guide your efforts.
- Understand Your Current State: Conduct a thorough assessment of your current technology infrastructure, processes, and workforce capabilities. Identifying strengths and weaknesses will help you determine where digital transformation efforts should be concentrated.
- Invest in Talent and Skills: Develop a strategy for acquiring and nurturing the right talent. This may involve upskilling current employees, hiring new digital experts, or partnering with external consultants. A skilled workforce is crucial for implementing and sustaining digital initiatives.
- Create a Culture of Innovation: Foster a culture that embraces innovation and change. Encourage employees to experiment, take calculated risks, and learn from failures. An innovative culture is key to adapting to evolving technologies and market dynamics.
- Collaborate and Partner: Collaboration with industry peers, startups, and technology partners can accelerate your digital transformation efforts. Look for opportunities to share knowledge, access new technologies, and leverage external expertise.
- Agile Approach: Embrace agile methodologies in your project management approach. Break down transformation initiatives into smaller, manageable projects, and iterate based on feedback. This flexibility enables you to adapt to changing circumstances.
- Manage Change Effectively: Implement a comprehensive change management strategy to help employees adapt to new processes and technologies. Provide training, support, and a clear roadmap for the transition.
Remember that digital transformation is not a one-time project but an ongoing journey. Technology and market trends will continue to evolve, so it’s essential to remain agile and adaptable. By following these guidelines and continuously assessing your progress, your organization can navigate the digital transformation journey successfully and stay competitive in an ever-changing business landscape.
Conclusion
In conclusion, Industrial Digital Transformation represents a profound shift in how industries operate and compete in the modern world. It encompasses the integration of digital technologies, data analytics, and automation into various facets of industrial processes, with the aim of enhancing efficiency, productivity, and competitiveness. This transformative journey offers numerous benefits, including improved operational efficiency, better decision-making through data analytics, enhanced product quality, and greater adaptability to changing market conditions.
However, the path to successful Industrial Digital Transformation is not without its challenges. Organizations must address workforce skill gaps, manage change effectively, and prioritize cybersecurity and data privacy. Clear objectives, strong leadership support, and a culture of innovation are also essential components of a successful transformation strategy.
The importance of Industrial Digital Transformation cannot be overstated in today’s rapidly evolving business landscape. Organizations that embrace this journey position themselves for long-term success, increased competitiveness, and the ability to meet the ever-changing demands of their customers and markets. As technology continues to advance, Industrial Digital Transformation remains a critical strategy for industries looking to thrive in the digital age.